Gas Ejector Design Calculation - The Key to Efficient and Reliable Gas Ejector Systems
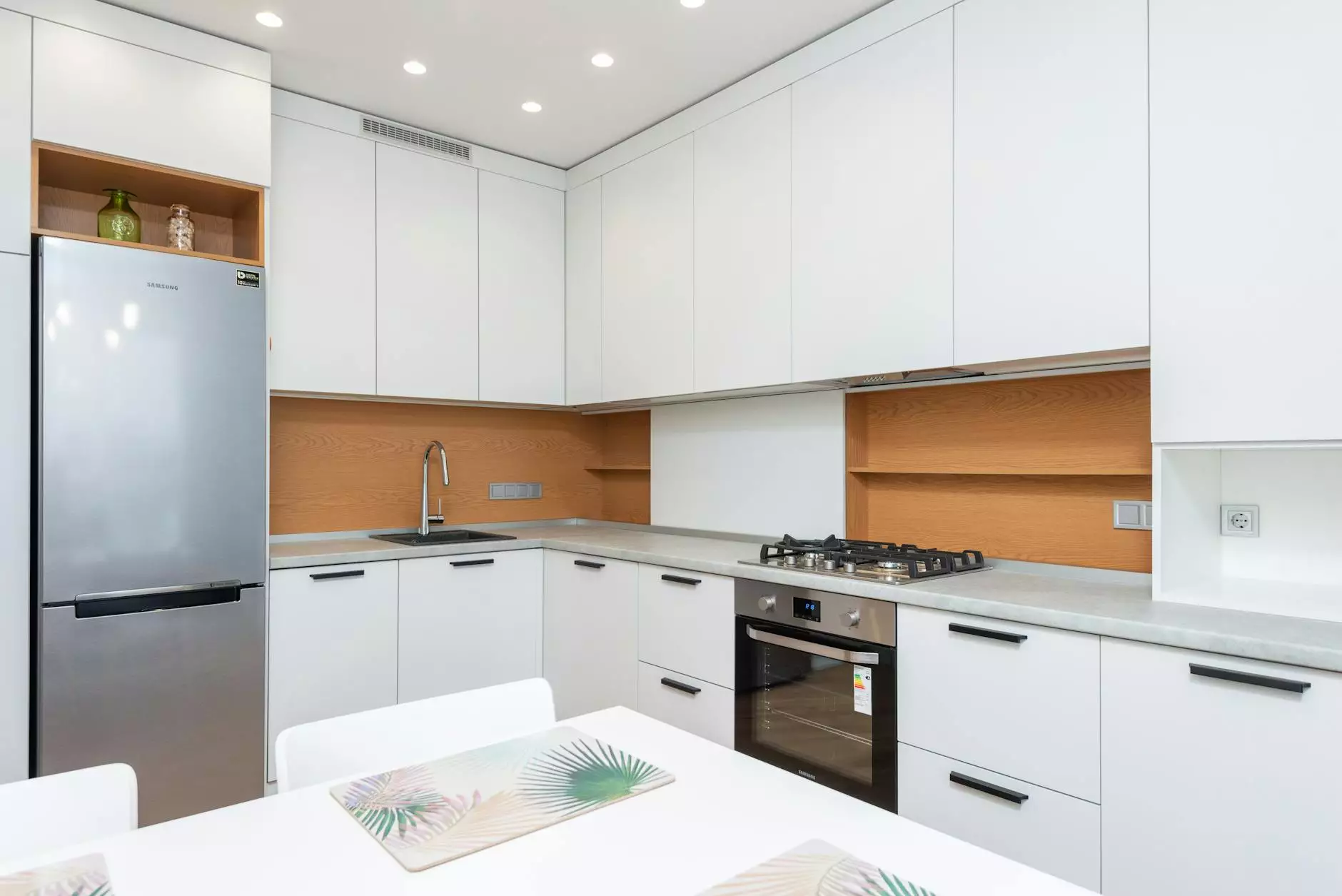
Gas ejectors are widely used in various industries for a range of applications, including gas compression, mixing, and ventilation. Understanding the importance of proper gas ejector design calculation is crucial for achieving optimal system performance, efficiency, and reliability. In this article, we will delve into the details of gas ejector design calculation and explore its significance in the context of gas ejector systems.
Introduction to Gas Ejector Systems
Gas ejectors, also known as ejector pumps or jet pumps, operate based on the principle of fluid dynamics and the Bernoulli's principle. These devices utilize the energy of a high-pressure fluid (the motive fluid) to create a vacuum and entrain a secondary fluid (the suction fluid) into the system.
Gas ejector systems find application in industries such as oil and gas, chemical, petrochemical, pharmaceutical, and HVAC. They are used for processes such as gas compression, gas scrubbing, venturi scrubbing, steam deaeration, and more. The efficiency and reliability of these systems depend heavily on proper design calculations.
The Significance of Gas Ejector Design Calculation
Gas ejector design calculation involves a thorough analysis of various parameters and factors that influence the performance of the system. These calculations help in determining the appropriate dimensions, specifications, and operating conditions for the gas ejector, ensuring optimal functionality.
Efficiency: Correct design calculations lead to highly efficient gas ejector systems. By accurately calculating the required motive fluid flow rate, suction fluid entrainment ratio, and operating pressures, engineers can eliminate inefficiencies and maximize the system's performance.
Reliability: A well-designed gas ejector system is reliable and performs consistently under varying conditions. Design calculations take into account the system's ability to handle pressure drops, temperature fluctuations, and variations in suction fluid properties. This ensures the longevity and dependability of the system.
Cost-effectiveness: Proper gas ejector design helps in optimizing the use of resources, minimizing energy consumption, and reducing maintenance costs. Accurate calculations prevent oversized or undersized equipment, ensuring the system operates at its peak efficiency, saving both energy and money.
Key Parameters in Gas Ejector Design Calculation
Motive Fluid Flow Rate:
The motive fluid flow rate is a critical parameter that determines the suction capacity and performance of the gas ejector system. It is crucial to calculate this value accurately, considering the desired suction fluid flow rate and the pressure conditions.
Suction Fluid Entrainment Ratio:
The suction fluid entrainment ratio defines the ratio of suction fluid drawn into the system compared to the motive fluid flow rate. Proper calculation of this ratio ensures optimum entrainment, avoiding excessive load on the ejector and maintaining efficient system operation.
Nozzle and Diffuser Design:
The design of the ejector's nozzle and diffuser sections significantly impacts its performance. Careful calculation of these components considers factors such as fluid velocity, pressure profiles, and flow characteristics. This results in an optimized design that minimizes losses and enhances ejector efficiency.
Operating Pressure:
Understanding the operating pressure conditions and pressure drop across the gas ejector system is vital for maintaining stability and preventing potential issues. Precise calculations determine suitable materials of construction, wall thicknesses, and fluid properties, ensuring safe and reliable operation.
The Role of Simulation and Advanced Tools
Simulation software and advanced design tools have revolutionized the field of gas ejector design. These tools enable engineers to simulate gas ejector performance, visualize complex fluid flows, and optimize designs before the actual implementation.
Utilizing computational fluid dynamics (CFD) simulations and other advanced techniques, engineers can analyze factors like flow distribution, velocity profiles, pressure recovery, and system behavior under different operating conditions. This simulation-driven approach greatly streamlines the design process and facilitates the selection of optimal gas ejector configurations.
In Conclusion
Gas ejector design calculation is a crucial aspect of developing efficient and reliable gas ejector systems. Accurate calculations help engineers optimize performance, enhance system reliability, and achieve cost-effectiveness by minimizing energy consumption and maintenance costs.
By focusing on parameters such as motive fluid flow rate, suction fluid entrainment ratio, nozzle and diffuser design, and operating pressure, engineers can deliver gas ejector systems that excel in performance and meet the demanding requirements of various industries.