Silicone Membrane for Vacuum Forming: Elevate Your Production Standards
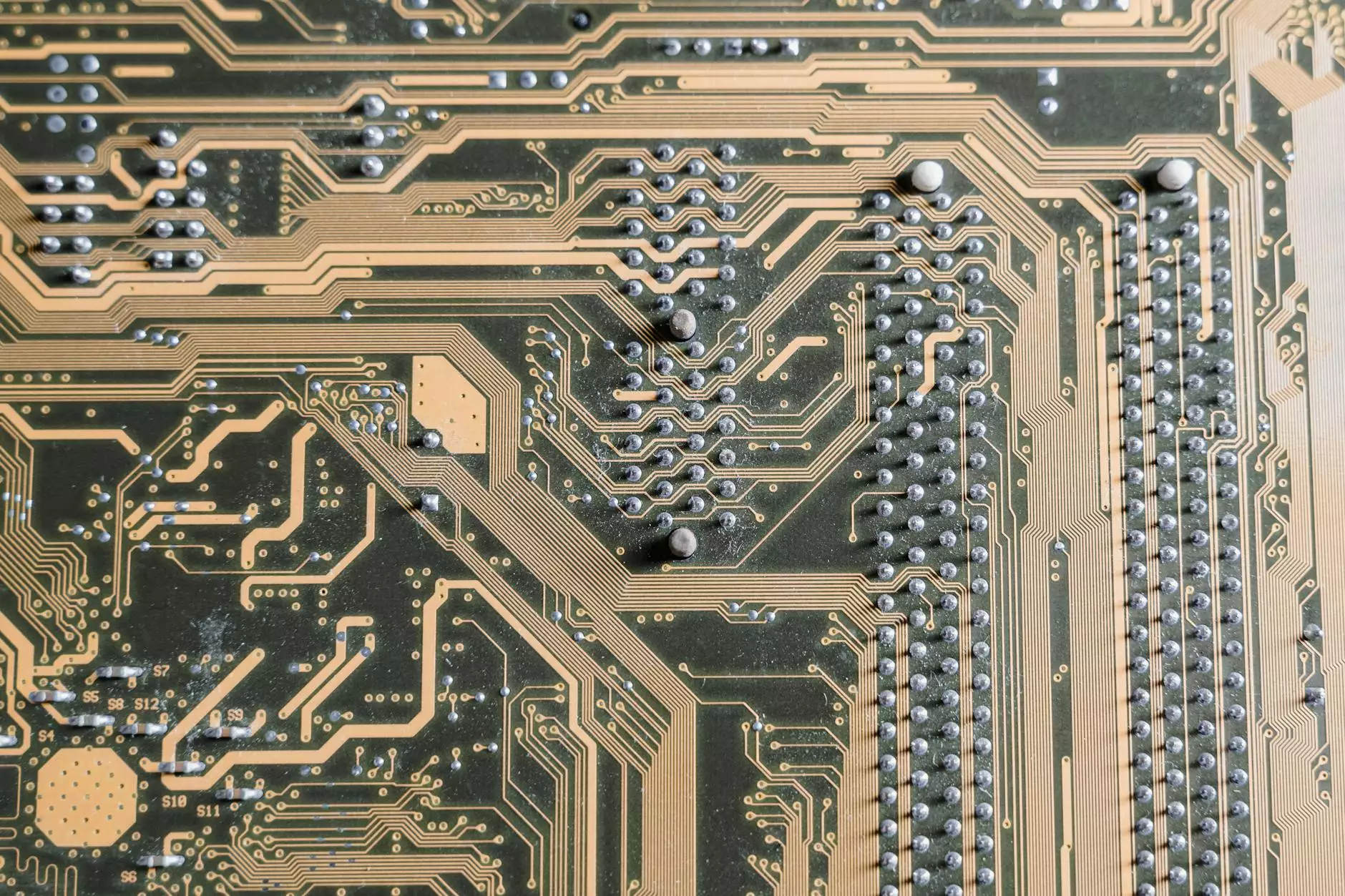
The world of manufacturing and product design has witnessed significant advancements over the years. One of the crucial innovations in this field is the silicone membrane for vacuum forming, a material that has revolutionized how products are shaped and formed. This article aims to explore the multifaceted benefits of silicone membranes specifically for vacuum forming, particularly for businesses in the Appliances & Repair and Home Cleaning sectors.
Understanding Vacuum Forming
Vacuum forming is a widely used manufacturing process that involves heating a thermoplastic sheet until it is pliable, then draping it over a mold. A vacuum is applied, sucking the sheet down onto the mold to take its shape. This process is celebrated for its efficiency and versatility, making it ideal for producing a variety of components, particularly in the appliance and home cleaning industries.
Key Components of Vacuum Forming
The essential tools in vacuum forming include:
- Molds: Typically made from materials like aluminum or wood, molds determine the final shape of the product.
- Heating Element: A heating system that softens the plastic sheet to make it malleable.
- Vacuum System: The equipment that applies suction to pull the plastic onto the mold.
- Silicone Membrane: An essential component that creates a seal and ensures consistent molding.
The Role of Silicone Membrane in Vacuum Forming
The silicone membrane for vacuum forming plays a pivotal role in achieving precise and high-quality products. Its unique properties make it an excellent choice for forming applications:
1. Flexibility and Durability
Silicone membranes are incredibly flexible, allowing them to conform to various mold shapes easily. This flexibility, coupled with their durability, ensures that they can withstand repeating cycles of heating and cooling without losing their effectiveness.
2. Temperature Resistance
An essential trait of a silicone membrane is its high-temperature resistance. Unlike other materials, silicones can endure the significant heat involved in the vacuum forming process, making them ideal for producing items in high-temperature appliances and equipment.
3. Low Friction Properties
The low friction nature of silicone enables easy release of the formed items from the molds, thereby minimizing damage and preserving product integrity. This aspect is particularly important in high-volume production environments where efficiency is key.
Applications of Silicone Membranes in Business
1. Appliances & Repair
In the appliances sector, silicone membranes are invaluable in the creation of various parts, such as:- Kitchen appliances: Silicone membranes are used to form components for blenders, toasters, and microwaves.- Home maintenance tools: They assist in producing durable parts for vacuum cleaners and other cleaning tools.
2. Home Cleaning Products
The home cleaning industry benefits from silicone membranes through:
- Custom molds: Crafting specific shapes for ergonomic cleaning tools that enhance user experience.
- Durability: Ensuring that cleaning products withstand the rigors of use over time.
Advantages of Using Silicone Membrane for Vacuum Forming
Businesses can unlock numerous advantages by incorporating the silicone membrane for vacuum forming in their production processes:
1. Enhanced Product Quality
The precision offered by silicone membranes translates into better-finished products. The fine details captured during the vacuum forming help distinguish high-end goods from standard offerings.
2. Cost-Effectiveness
Although the initial investment for silicone membranes may be higher than alternative materials, they offer long-term savings through reduced wear-and-tear, fewer replacements, and enhanced efficiency in the molding process.
3. Environmentally Friendly Options
Many silicone membranes are produced with sustainability in mind. This environmentally friendly approach appeals to conscious consumers and businesses striving to reduce their carbon footprint.
Tips for Choosing the Right Silicone Membrane
Selecting the right silicone membrane for vacuum forming requires understanding your specific needs. Here are some considerations:
- Thickness: Depending on your molding requirements, choose a thickness that balances flexibility and durability.
- Type of Silicone: Different silicones offer different benefits; research and choose the one that aligns with your production goals.
- Supplier Reputation: Work with reputable suppliers with a proven track record in delivering quality materials.
Conclusion
In summary, the silicone membrane for vacuum forming is an indispensable asset for businesses operating in the Appliances & Repair and Home Cleaning industries. Its versatility, durability, and cost-effectiveness contribute to enhanced production capabilities and superior product quality. By embracing silicone membranes, businesses not only improve their operational efficiency but also cater to the evolving demands of the market. Equip your business with this innovative solution and witness the transformation in your production line.
For more information on high-quality silicone membranes and vacuum forming solutions, visit vacuum-presses.com.