The Comprehensive Guide to Concrete Mixing Plants
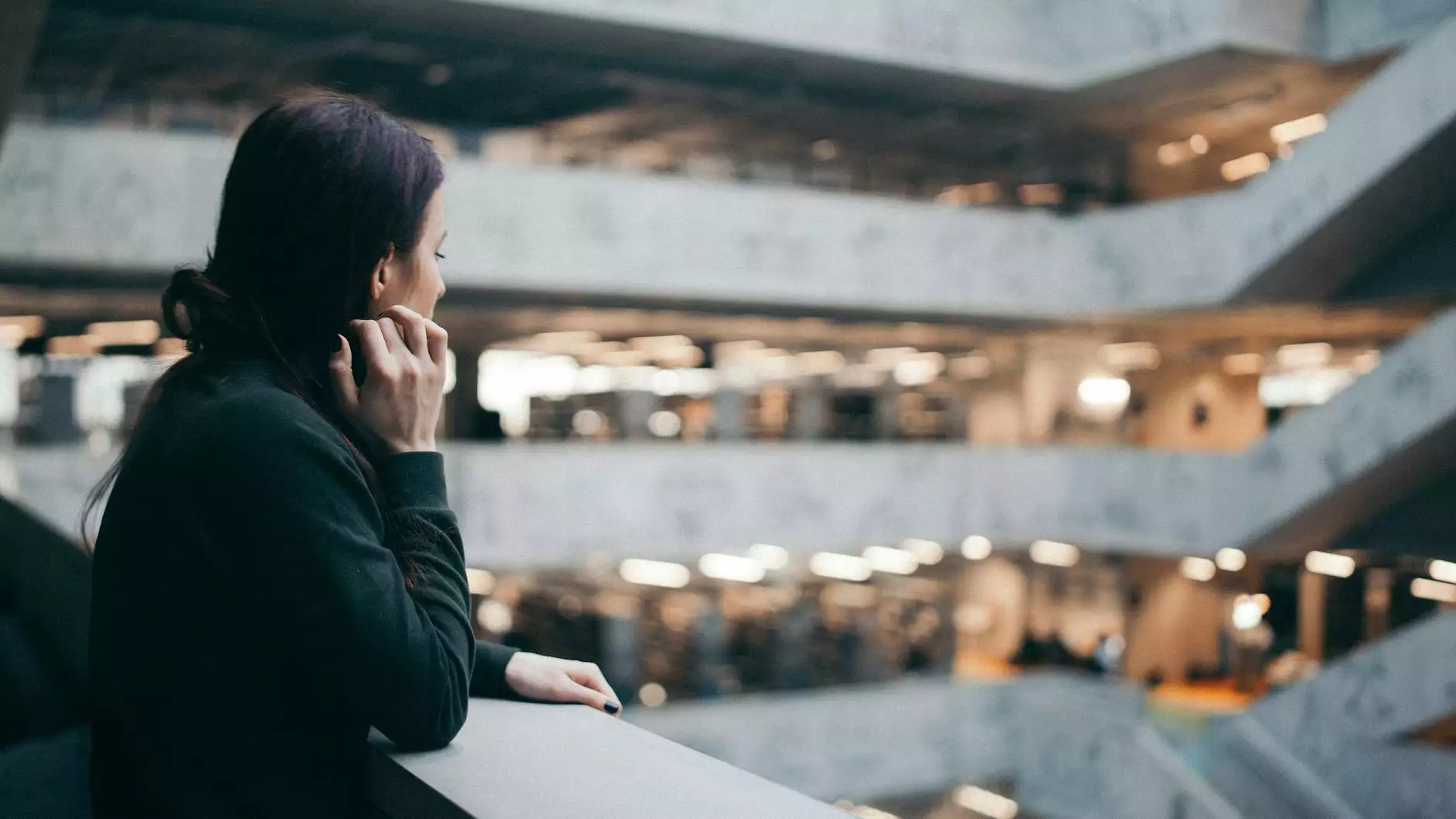
Understanding Concrete Mixing Plants
A concrete mixing plant is a vital facility in the construction industry, responsible for the production of concrete through a systematic mixing of various materials. These plants serve as the backbone of various construction projects, supplying high-quality concrete necessary for building foundations, bridges, pavements, and more. This article delves deep into the workings, advantages, and innovative features of modern concrete mixing plants, particularly focusing on the offerings from Polygon Machinery.
The Components of a Concrete Mixing Plant
A concrete mixing plant consists of several key components, each playing an essential role in the production process. Understanding these components is crucial for anyone involved in the field. The primary elements include:
- Aggregate Bins: Contain various materials like sand, gravel, and crushed stone.
- Batching Scale: Accurately measures the required amount of each material.
- Concrete Mixer: The heart of the plant that combines all the materials to produce concrete.
- Control System: Allows for the automation and monitoring of operations, ensuring precision in the mixing process.
- Silo: Storage for cement and other powdered materials.
How Concrete Mixing Plants Operate
The operation of a concrete mixing plant can be divided into several stages:
- Material Batching: Precise quantities of aggregate, cement, and water are loaded into the batching scale.
- Mixing: Once batched, the materials are transferred to the concrete mixer. The mixing duration and speed can be adjusted based on the required consistency.
- Discharge: The mixed concrete is discharged into trucks or storage areas for transport to the construction site.
Types of Concrete Mixing Plants
There are several types of concrete mixing plants, tailored to meet various production needs:
- Stationary Mixing Plants: Ideal for large-scale projects requiring a constant supply of concrete.
- Mobile Mixing Plants: Flexible and easy to transport, these plants are perfect for smaller projects or locations that change frequently.
- Continuous Mixing Plants: Designed for uninterrupted operation, suitable for high-volume production.
Benefits of Using Concrete Mixing Plants
The advantages of utilizing a concrete mixing plant are multifaceted. Here are some key benefits:
- Quality Control: Automated batching and mixing processes ensure consistent quality of concrete.
- Efficiency: High production capacity translates to better project timelines and resource management.
- Cost-Effectiveness: Reduced labor and material wastage results in lower operational costs.
- Customization: Modern plants can produce various concrete mixtures to meet specific project requirements.
Innovations in Concrete Mixing Technology
The field of concrete mixing is constantly evolving. Innovations that enhance production efficiency and environmental sustainability are leading the way. At Polygon Machinery, we prioritize advanced technologies that streamline processes. Some significant recent innovations include:
- Smart Mixers: Integrated IoT devices that monitor the mixing process in real time, optimizing for consistency and quality.
- Green Concrete Solutions: Research and development in eco-friendly materials and techniques reduce the environmental impact of concrete production.
- Automated Systems: Robotics for loading, unloading, and transporting concrete, significantly lowering labor costs and enhancing safety.
The Role of Electronics in Concrete Mixing Plants
As technology advances, the integration of electronics in concrete mixing plants becomes increasingly significant. Sophisticated electronic systems facilitate:
- Real-time Monitoring: Integrated sensors provide data on material levels, temperature, and humidity, ensuring optimal mixing conditions.
- Remote Control: Operators can manage the mixing process from a distance, minimizing the need for on-site personnel.
- Data Analytics: Leveraging data for predictive maintenance and operational efficiency, prolonging the lifespan of equipment.
3D Printing and Its Impact on Concrete Production
Another cutting-edge development is the use of 3D printing within the concrete industry. This technology allows for the creation of complex structures with precision, reducing material waste and labor costs. At Polygon Machinery, we invest in aligning our concrete mixing plants with 3D printing technologies:
- Customized Designs: 3D printing allows for unique architectural designs that were previously difficult to achieve.
- Rapid Prototyping: Faster time from concept to build, which is critical in a competitive construction landscape.
- Material Efficiency: Reduced waste and lower resource consumption compared to traditional construction methods.
Conclusion
In summary, a well-designed concrete mixing plant is essential to the construction industry, offering numerous benefits such as improved quality, efficiency, and cost-effectiveness. With Polygon Machinery at the forefront of technological advancements in this sector, we continue to redefine standards and set benchmarks for excellence.
Whether you are involved in large-scale construction or smaller projects, understanding the intricacies of a concrete mixing plant will empower you to make informed decisions that enhance your operational capacity and product quality. The future of construction is here, and it is powerfully entwined with innovations in concrete mixing technology.